Knelpunten elimineren en targets halen
Proces optimalisatie heeft tot doel om knelpunten te elimineren en targets te halen binnen de gewenste tijd en het vastgestelde budget. Een project om processen te optimaliseren geeft bovendien het inzicht om realistische targets en budgetten te bepalen.
Soms is het eenvoudig te ontdekken waar en hoe een knelpunt ontstaat in een logistiek proces. In complexere operaties is dat vaak minder eenvoudig. Daar moeten de consequenties van veranderingen voor het geheel aan processen bekeken worden om het ontstaan van nieuwe knelpunten in andere processen te voorkomen.
Vijfstappenplan voor proces optimalisatie
Het plan voor het optimaliseren van een of meer processen in het magazijn kent vijf stappen.
De volgende stappen tot proces optimalisatie zijn altijd van toepassing. Of het proces dat geoptimaliseerd dient te worden nu wel of niet inzichtelijk gemaakt is.
Stap 1: Breng het proces in kaart
De eerste stap tot proces optimalisatie is het in kaart brengen van het proces. Bij het optimaliseren van meerdere processen of het geheel aan processen wordt deze stap voor elk afzonderlijk proces uitgevoerd.
Met behulp van een proces analyse wordt het proces in kaart gebracht. De uitvoering van een proces analyse wordt ook behandeld in het kennisbankartikel “hoe richt ik mijn magazijn optimaal in”.
Hoe pak je proces optimalisatie aan?
Allereerst is het noodzakelijk om de juiste kennis van de processen te vergaren. Dit is mogelijk door rond te lopen in het magazijn, mee te kijken en te werken met de processen, veel vragen te stellen en aantekeningen te maken.
De opgedane kennis moet vervolgens visueel in kaart worden gebracht. Dit kan met behulp van een proces flowchart (ook wel processchema genoemd). Een proces flowchart is een grafische weergave van een proces. Met de opgedane kennis van de logistiek en het omzetten van deze kennis naar een flowchart is de proces analyse afgerond.
Het geheel aan in kaart gebrachte processen maakt ook de relatie tussen de processen duidelijk.
Stap 2: analyseer de juiste data
De volgende stap tot proces optimalisatie is het uitvoeren van een data analyse. Met de data analyse wordt de frequentie van het uitvoeren van het proces inzichtelijk gemaakt. Dit gaat om de frequentie van het totale proces, maar ook per processtap. Zowel de frequentie van het proces, als de procestijden zijn bepalend om te achterhalen welk proces of deelproces geoptimaliseerd moet worden.
Bij een data analyse is het noodzakelijk om hiervoor representatieve data te gebruiken. Neem de data van een geheel kalenderjaar of zelfs meerdere jaren om de juiste conclusies uit de data analyse te kunnen trekken.
Let bij het selecteren van representatieve data op:
- Extreme waarden (uitschieters)
- Seizoensinvloeden
- Excepties (uitzonderingen)
Mochten deze zaken zich voordoen in de data, dan kan dit zorgen voor een vertekend beeld van de dagelijkse operatie. Zowel in de analyses als in de eindconclusies die de basis vormen voor de gewenste verbeteringen.
Stap 3: Vind de verspilling in het deelproces
Met behulp van de proces- en data analyse kan het knelpunt geïdentificeerd worden. Wanneer het knelpunt geïdentificeerd is, moet achterhaald worden wat de oorzaak hiervan is. Die kan achterhaald worden door in te zoomen op het deelproces en te kijken welke specifieke verspillingen zich daar voordoen.
8 manieren van verspilling - Lean Six Sigma
Taiichi Onno kwam met het acroniem “TIM WOODT” om de 8 manieren van verspillingen bij TOYOTA te definiëren. Dit is onderdeel van het welbekende Lean Six Sigma dat in veel logistieke operaties wordt toegepast.
Lean Six Sigma - 8 manieren van verspillingen
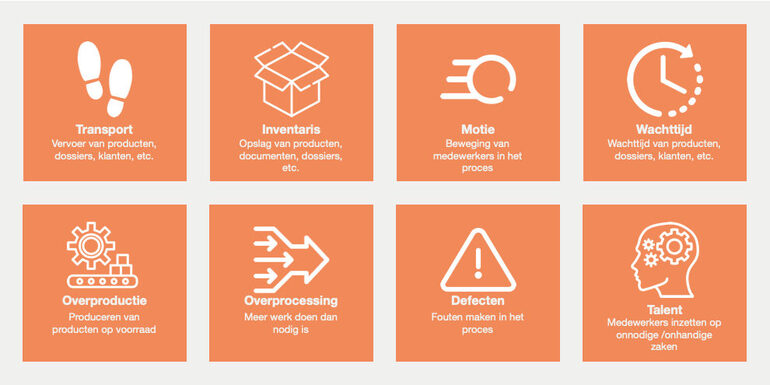
Veel voorkomende verspilling in de logistiek
Een voorbeeld van veel voorkomende verspilling is te veel bewegen van medewerkers (Motie). Te lange loopafstanden of rij-afstanden bij het orderpicken. Dit kan veroorzaakt worden door een inefficiënte orderpickroute, geen tot onvoldoende of onduidelijke werkinstructies, veel zoekwerk, lage voorraadbetrouwbaarheid, verkeerd of te laat replenishen enz.
Het is dan ook essentieel om na de vaststelling van de aard van verspilling de oorzaak of oorzaken vast te stellen.
Stap 4: Ontwerp het optimale proces
Nu is inzichtelijk
- welk (deel)proces geoptimaliseerd moet worden
- wat het knelpunt precies is
- wat dit veroorzaakt
De volgende stap is het bedenken van het verbeterde proces.
Neem in dit ontwerpproces altijd het betrokken personeel mee. Met name de medewerkers die het logistieke proces uitvoeren. Door samen vanuit de praktijk over de verbetering na te denken komen de beste ideeën naar voren. Daarnaast wordt er alvast een draagvlak gecreëerd bij diegenen die uiteindelijk het verbeterde proces zullen uitvoeren en raakt men van begin af aan vertrouwd met de nieuwe werkwijze.
Zo wordt ook duidelijk wat verandert (en waarom) en wat blijft zoals men gewend was.
Praktijkvoorbeelden van proces optimalisatie
In stap 3 is het voorbeeld gekozen van verspilling door te lange loopafstanden bij het orderpicken. Vaak is de oorzaak hiervan een inefficiënte indeling van het pickmagazijn, waarbij artikelen niet op basis van omloopsnelheid zijn ingedeeld.
ABC analyse: wat is de omloopsnelheid van een artikel?
Om deze verspilling tegen te gaan kan er een ABC-analyse (analyse om de omloopsnelheid van de artikelen te bepalen) uitgevoerd worden.
Met de uitkomsten van deze analyse kan het magazijn opnieuw ingedeeld worden op basis van omloopsnelheid. Hierdoor liggen de artikelen die snel lopen vooraan in het magazijn opgeslagen.
Artikelen die nauwelijks of zelfs niet lopen kunnen helemaal achteraan opgeslagen worden.
Meer verbeteropties voor hetzelfde knelpunt
Bij verspilling door te lange loopafstanden kan verandering van het pickproces een optie zijn. Orderpicken in batches of waves bijvoorbeeld. Hierdoor worden er meerdere orders tegelijkertijd gelopen, waardoor de loopafstand per order dus ook gereduceerd wordt.
Mechanisatie/automatisering kan ook een oplossing zijn. Bijvoorbeeld door de goederen naar de medewerker te laten komen. ‘Goods to man’ in plaats van ‘man to goods’.
Zo kies je de juiste optie
Bij dit soort oplossingen is het altijd noodzakelijk om een business case te maken en de investering af te zetten tegen de besparingen (ROI). Hoeveel kost je proces nu, hoeveel bespaar je door de beoogde mechanisatie/automatisering en hoe lang is de terugverdientijd? De antwoorden hierop bepalen of een mechanisatie/automatisering oplossing de juiste optie voor verbetering zijn.
Per proces of deelproces kunnen er meerdere verbeteropties zijn. Om de juiste keuze te maken wegen o.a. de volgende factoren mee:
- Urgentie (hoe hoog is de nood)
- Aard van het bedrijf en de rol van de logistiek
- Budget
- Tijdsdruk (alles in 1x aanpakken of faseren)
Stap 5: Implementeer het verbeterde proces
Bij de implementatie is het noodzakelijk om de proces optimalisatie te waarborgen. Het personeel zal immers een nieuwe manier van werken moeten leren. Er zijn een aantal manieren om de nieuwe werkzaamheden duidelijk onder het personeel te communiceren, zodat er gewerkt wordt naar de nieuwe inrichting van het proces.
Denk hierbij onder andere aan:
- Het maken van duidelijke werkinstructies (welke talen/visueel)
- Voldoende magazijnsignalisatie (belijning, locatiestickers, brandveiligheidsborden, etc.).
- Sturing en handhaving door teamleaders/managers.
Daarnaast is het bij het doorvoeren van een verandering binnen een organisatie van belang om te focussen op change management. Hoe beter de verandering gemanaged wordt, des te beter zal de transitie verlopen. Goed change management vanaf de eerste stappen in het optimalisatie project zorgt ook voor minder weerstand van personeel en/of de organisatie.
Continuous improvement - borging
Blijf na de implementatie het proces monitoren op effectiviteit.
Het monitoren is mogelijk door bijvoorbeeld gebruik te maken van een KPI-dashboard. Op deze manier kan er op tijd bijgestuurd worden of, als de resultaten tegenvallen, zelfs opnieuw gekeken worden naar de proces optimalisatie.
Hierdoor kunnen ook eventuele “bugs” in het proces geïdentificeerd en geëlimineerd worden. Track dus altijd de resultaten van de proces optimalisatie en reageer op de uitkomsten.
Hoe succesvol is de verbetering?
Of het nu om de verbetering van een (deel)proces gaat of het geheel aan logistieke processen: het resultaat bepaalt of de aanpak en investering aan geld, tijd en energie succesvol is geweest. Daarom is het belangrijk het proces te blijven monitoren. Zo kan worden vastgesteld hoe het resultaat van de efficiencyverbetering zich verhoudt tot de gemaakte kosten.